Battery Technologies
Basic Concepts in Battery Technologies
Energy Density:
It is the amount of electrical energy that the battery can store per unit weight or unit volume.
“Gravimetric energy density” specifies how many Wh (watt hours) energy can be stored in a 1 Kg battery and is indicated in Wh / Kg unit.Some manufacturers also use units such as Ah / Kg to convert this unit to energy with the polar voltage of the corresponding battery Ah / Kg value must be multiplied.
“Volumetric energy density” indicates “how many Wh energy can be stored in 1 Liter volume and Wh / Lt. shown as. "High energy density" is desired in batteries.
Charge efficiency:
In other words, this parameter, also called "Energy efficiency", is defined as the ratio of the amount of energy drawn from a fully charged battery until it is fully discharged to the amount of energy given to the battery to fully recharge the same battery.
It is less than 100%. It is desired to be as high as possible. As a result, the difference between the energy given during charging and the energy drawn in discharging from the battery is an energy "lost" in the battery.
Dept of Discharge-DoD:
It is the rate of battery discharge from 100% full to 0% fully discharged. 80% DoD means that the battery is discharged to 80% of its capacity stated in Ah.
State of Charge-SoC:
It expresses the charge rate of the battery in%. Generally, the relationship between the voltage at the battery terminals and the SoC value varies according to the technology of the battery.
Cycle Life:
A “cycle” is when the battery is discharged to a certain level of DoD and then fully charged. If the battery can be put into charge / discharge "cycle" to maintain its capacity, which is stated as Ah, up to 80%, the "cycle life" of that battery is equal to that number. That is, the number of times a X Ah battery is discharged to a capacity of 0.8 X Ah. number is the number of cycle lives. However, in the display of the cycle life number, the operating temperature and DoD values must also be stated together. For example, the cycle life at 20% DoD and 25 °C, and the cycle life at 80% DoD and 40 °C can be very different numbers.
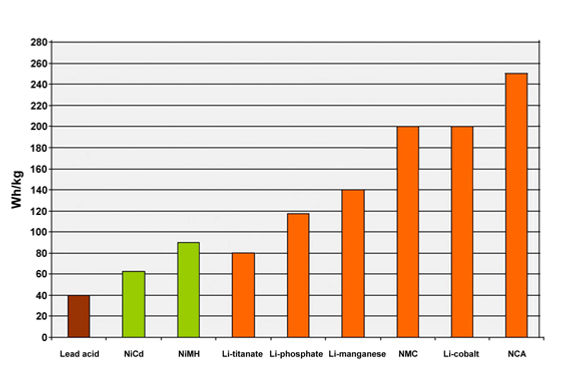
Lead Acid Batteries
Electro Chemical Structure
Lead-acid is one of the oldest and most developed battery technologies. It is the most popular electricity storage alternative due to its power quality and affordable cost.
The relatively low charge / discharge cycle lifetimes (500-800) constitute its main drawback. 25-40 Wh / kg (Gravimetric) and 60-75 Wh / lt. They have an acceptable performance with (volumetric) energy density and 80-90% charging efficiency.
Chemical Reaction During Discharge
The lead oxide (PbO2) material forming the positive plate has electrically high potential (1.69V) and the lead (Pb) material forming the negative plate, on the contrary, has low potential (-0.358 V). When the poles of the battery are connected to a charge that can flow electric current, this potential difference between the plates causes ionization in the electrolyte, causing the sulfuric acid (H2SO4) and water (H2O) molecules to split into ions and form H +, SO42-, OH-.
H2SO4 -> 2H +, SO42- H2O -> H + + OH-
In this process, positive ions (H +) begin to flow towards the positive electrode, and negative ions (OH-) to the negative electrode, and this causes a positive electrode to negative current to form in the battery. In this context, a "reduction" reaction occurs at the positive electrode and an "oxidation" reaction at the negative electrode.
Positive Electrode: PbO2 + 4H + + SO42- + 2e -> PbSO4 + 2H2 O
Negative Electrode: Pb + SO42- -2e -> PbSO4
Oxygen Recombination
There are passageways in the separating material ( AGM or Gel) between the positive and negative plates to allow gas passage. Oxygen produced in the positive plate during charging passes through these passages to the negative electrode, and before the hydrogen leaves the plate, it reacts with the spongy lead plate. In this way, oxygen combines with hydrogen (recombination) and returns to the electrolyte as water.
On the other hand, due to the formation of PbSO4 in the negative plate, the polarization potential decreases and by preventing the formation of hydrogen gas, VRLA does not cause an increase in pressure that will cause gas output from the valves in the battery.
O2 + H2SO4 + 2Pb -> 2PbSO4 + 2H2O
Electrical Properties
During basic chemical reactions, electrodes composed of lead and lead dioxide physically change shape due to the binding and dissolution of ions during discharge. These changes cause the plates to lose material over time and therefore not to perform as well as before.
While lead acid batteries show good performance around 20 °C, after the temperature exceeds 40 °C (especially AGM batteries), they are not suitable to be operated in very hot conditions because of permanent damage to the electrolyte and electrode plates. Basically, every 10 °C increase in temperature causes the life of the battery to be halved. Since it is not practical to replace the electrolyte and lead electrodes especially in VRLA type batteries, operating the battery under high temperature conditions seriously reduces their life.
Batteries with different polarity voltages such as 6V, 12V, 24V are produced by making serial internal connections in "cells" with open circuit voltage around 2.1-2.2 V in Lead Acid batteries.
Discharging cell voltages with care not to drop below 1.80V extends their life. Batteries, which are frequently "deeply discharged" below 1.7 V, cannot store as much energy as they used to when they are recharged. This causes the battery capacity, which should be 100 Ah, to drop to 90, 80 or 60 Ah over time, for example.

- Ah (Ampere hour) values written on the labels of VRLA batteries are written as the capacity value that will show the current that the battery cell voltage can give in 10 hours discharge at 20 °C until the battery cell voltage drops to 1.8V. This is denoted as C10. In other words, when 100 A is continuously drawn from a battery specified as 1000 Ah C10 for 10 hours, the battery cell voltage drops to 1.8 ".
Similarly, there are C2, C5, C20 type batteries. As the x value in the Cx unit decreases, the amount of current that the battery can deliver in the same period increases. In other words, 200 A can be drawn from the battery that is given 1000 Ah as C5 for 5 hours. Therefore, the smaller the x, the higher the quality and price of the battery.
- The parameter "C / x" is used to express the discharge current in the documentation and literature of some manufacturers. Where C is the Ah capacity value of the battery, and x is how many hours it will be discharged. For example, for a 100Ah battery, "when discharged with C / 4" means to discharge with 100/4 = 25 A.
- While graphing the charge and discharge currents in battery catalogs, parameters in the form of Ix are used. For example, for a 2V 1000 Ah battery, the I10 value is 100 A. In this context, in a given charge curve, when it is said "it is the graph when it is charged with a value of 0.2 I10", it is meant to say when it is charged with a constant current of 20 A, which is equal to 20% of this current value.
Values such as I10 given for charging currents in the battery catalogs mean 100/10 = 10A for the battery, for example, where the battery is 100Ah according to the C10 capacity rating. Manufacturers give a maximum value for charging current (such as 2.5 x I10). Also graphs are given for various multiples and fractions of I10 (figure below).

Accordingly, if 20% of its capacity is charged with I10 current, it will reach 2.4V limit voltage in about 3 hours. For this, follow the red line that says 0.2. Similarly, a 100% discharged battery can be charged by following a curve of 1.0, for example, with 2 times the I10 current to 2.4V charge cut-off voltage in 6 hours.
In AGM ( Absorbed Glass Mat ) type VRLA batteries, it is impregnated with a cloth made of electrolyte fiber fibers containing 1/3 acid and 2/3 water and squeezed between the electrodes. In this way, the battery becomes resistant to vibrations and there is no liquid electrolyte in the environment. In gel type batteries, the electrolyte is absorbed in a silicon dioxide based gel material and fills the electrode plates of the battery.

Fiber Glass Mat
Charge / discharge cycle life of gel batteries is approximately 2 times better than AGM batteries. However, they show worse performance than AGM batteries in applications that require sudden and high current due to their nature.
The volumetric energy density of AGM type batteries is better than Gel. On the other hand, deep discharge life of gel batteries is higher than AGM's.
AGM batteries cause less gas output than gel batteries. While gas recycling is 85-95% in gel batteries, this rate is 97% in AGM batteries.
Gel batteries perform better than AGM batteries at high temperatures. On the other hand, AGM batteries perform better than Gel batteries in conditions below zero degrees. A fully charged battery can be stored at lower temperatures than a discharged battery. For example, a fully charged battery can be stored up to -55 ..- 60 °C, while a discharged battery can be stored at a temperature as low as -20 ..- 25 °C.
Even if lead acid batteries are stored in charged state, Sulphate ions gradually start to stick to their plates over time. This is why batteries "self-discharge". Self-discharge characteristics of gel batteries are 2-3 times better than AGMs. While gel batteries discharge 20% in 1 year, AGM batteries can discharge 20-30% in 6 months.
Leaving lead acid batteries at low charge levels for long periods of time causes a phenomenon called "Sulfation". Lead Sulphate molecules first accumulate in amorphous form and turn into solid sulphate crystals if they are not charged. Sulfation that has not yet turned into a solid crystal is called "reversible sulfation". This situation occurs when the battery is left at low charge for 2-3 weeks without being charged. The amorphous sulphate layer formed can be recycled by "overcharge" the battery to correspond to 2.5 to 2.66 V / cell voltage after fully charged. In this way, sulfate ions break off from the lead and return to the electrolyte again. However, if sulfation lasts long enough to form solid crystals, "irreversible sulfation" occurs. Overcharge cannot dissolve solid sulphate crystals and the battery loses capacity as Ah. Because the SO4 ions required for ion transfer in charge / discharge are no longer in the electrolyte and the acid concentration in the electrolyte decreases because they do not react. This is perceived as a decrease in Ah capacity.
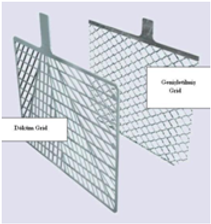
Lead Electrode Plates
Lead-Carbon Batteries
"Sulfation" in the PbO2 anode plate, which is an important problem in Lead-Acid batteries that have a cathode / anode pair containing Lead and Lead oxide, is an issue that has been tried to be solved for years as a factor that shortens the cycle life of the battery and increases the capacity loss. On the other hand, the advantage of Carbon anodes used in "Super Capacitor" applications is known. In recent years, with the technologies called "Advanced Lead Acid", the cycle life of the batteries has begun to be increased with the hybrid anode structures containing Lead-oxide / carbon versus Lead Cathode. This technology, which started to take place in the market with automobile starter batteries, will be used in stationary applications as it develops.
Lithium-ion Batteries
Lithium, an alkali metal, with atomic number 3, is the "smallest" atom of the periodic table after Hydrogen and Helium. Therefore, ion mobilization between Anode and Cathode in chemical reactions is very easy. It is capable of generating an E0 standard potential much higher than any other metal such as -3.04V when it gives off electrons.
Due to these features, Lithium has become one of the most preferred elements of rechargeable (secondary) battery technologies. Since Lithium Metal Oxide (Li-Ion) and Lithium Metal Phosphate based "cathode" (positive electrode) materials can provide a very high energy storage density as a rechargeable battery, it has made it a preferred technology especially in mobile equipment and electric vehicles (EV).
The element lithium is known as the 31st most abundant element in nature. Mining is carried out in the world, especially in China, North America, Brazil, Chile, Argentina, Russia, Spain, Afghanistan and some parts of Africa. Its reserves (excluding those that can be obtained from sea water) are estimated to be around 28.4 million tons. Relatively 0.17 ppm Lithium is present in 1.4 × 1021 kg sea water. In other words, the reserves of all seas contain 200 Billion Tons of Lithium. In this context, Lithium is not an element that will end quickly.
Basic characteristics of Lithium Metal Oxide Cathode type batteries, which are the most used types of Lithium-Ion batteries
- High energy density (270 Wh / lt, 220 Wh / kg)
High charging efficiency (~ 98%)
- Cycle life (500-1500 cycles @ 80% DoD)
In this type of batteries, the cathode is made of materials called "lithiated metal oxide" (LiCoO2, LiMnO4, LiNO2 etc.) and the anode consists of carbon graphite material in its surface structure.

The electrolyte material is from lithium salts (eg LiPF6) dissolved in organic carbonate (PC-Propylene Carbonate, EC-Ethylene Carbonate, DMC-Dimethyl Cabonate, DEC-Diethyl Carbonate). During charging, the lithium atoms in the cathode become ionized and pass through the electrolyte and reach the carbon anode and combine, giving current electron in the outer circuit. This process is reversed on discharge.
When Lithium Manganese Oxide (LiMnO4) is used instead of Lithium Cobalt Oxide (LiCoO2), the risk of explosion is eliminated in the overcharge created by Cobalt. However, when it goes above 50°C in this type of battery, the performance drops dramatically. On the other hand, when using Manganese (Mn), the energy density drops by 20%. However, Manganese is a much safer and more environmentally friendly element than Cobalt. However, cobalt based Li-Ion batteries are preferred due to their energy density.
When using Nickel Oxide (LiNiO2) metal, the energy density of the Li-Ion battery increases by 30% compared to cobalt. However, since the exothermic reaction that occurs on the other hand produces much higher heat, cooling problems occur in Nickel-based batteries. Tri-metal Lithium Nickel Manganese Cobalt Oxide - Li (NiCoMn) O2 (NMC) type is also produced in the industry and some parameters (1000-1500 cycles) that are both cheap and safe can be obtained. On the other hand, although the cycle life is low (500 cycles), energy densities of 200-250 Wh / kg can be reached by using Nickel-Cobalt-Aluminum Oxide - LiNiCoAlO2 (NCA) chemistry and NCA batteries can stand out in applications requiring "light" batteries.
Lithium-Ferrite Phosphate (LFP) Batteries
Another type of Lithium-Ion batteries, called Lithium-Iron Phosphate or Lithium Ferrite Phosphate in the market, the cathode material in these batteries is made of lithium metal phosphate material instead of lithium metal oxide. Iron, cobalt, manganese or titanium are used as metals.
Lithium Ferrite Phosphate battery technology was scientifically reported by Akshaya Padhi of Texas University in 1996. Lithium Iron Phosphate (LiFePO4) batteries, one of the most suitable in terms of performance and production, have started mass production commercially.
• High energy density (220 Wh / lt, 100-140 Wh / kg)
High charging efficiency (> 90%)
Long cycle life (> 2,000 cycles @ 80% DoD)
Good performance at high and low operating temperatures (-20 ... +55 °C)
Basic chemical reaction: LiFe (II) PO4 <-> Fe (III) PO4 + Li + e-
It is reported that the performance values are further improved with the cathode material produced in the form of "Nano Phosphate" by the American company A123. In new batteries with this model cathode, 90% charge capacity can be reached in 5 minutes. The same batteries are at 7000 (100% DoD) cycles but good enough to lose 20% capacity.
Silicone Nanowire Anode Lithium-Ion Batteries
Dr. It emerged with a method developed by Yi Cui and his team in 2007. In conventional Lithium-Ion batteries, when the anode made of carbon graphite is produced as silicon nano-wires, the deformation on the anode surface during the binding of Li ions in graphite or film silicon-based anodes during lithiation and their separation during discharge is reduced.
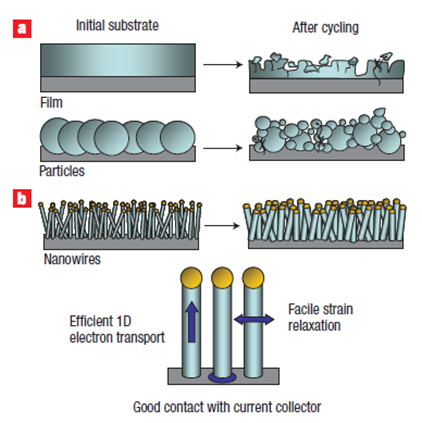
Silicon nanowire wires to which Li ions are bound become fat and their length increases. When the Li ions are separated, a very high rate of wires return to their original state. This technology will enable Li-Ion batteries to reach much higher energy density (8-10 times the current ones) and to be charged / discharged very quickly.
Lithium-Titanate Anode Li-Ion Batteries
Anode made of carbon-graphite in Lithium-Ion (Li Metal Oxide) batteries, Lithium-Titanate (Li2TiO3) batteries consist of Lithium Titanate crystals that have been turned into "nano-crystalline" thanks to nanotechnology. The most basic advantages of Lithium-Titanate batteries, developed by the "Altairnano" company, followed by Leclance (Switzerland) and Japanese companies such as Toshiba, Seiko and Yabo, compared to other battery types.
- Very high energy density (7500 Wh / lt, 4000 Wh / kg, 160 Ah / Kg)
- High charging efficiency (about 87-95%)
- Very long cycle life (15,000-25,000 cycles @ 80% deep discharge)
Low cell voltage: 2.4V nominal

Lithium Titanate nano crystals used in the anode increase the anode surface area to 100 m2 / gr. To compare, this ratio is at the level of 3m2 / gr in graphite anode used in Li-ion batteries. Lithium salts dissolved in the electrolyte substance organic carbonate are used. During charging, Lithium atoms in the cathode become ionized and Li2TiO3 passes through the electrolyte and reaches the anode and combines, giving its electron, creating a current in the outer circuit.
This process is reversed on discharge. The excess surface on the anode helps this type of batteries to be charged very quickly. In addition, it can perform quite well in low temperatures such as -30 °C. At the latest point of this technology, Li4Ti5O12 (Lithium Titanate Spinel) nanocrystals, a special crystal phase of Lithium Titanate, can discharge 10-100 times faster than existing Lithium Titanate cells.
Lithium Sulfur Batteries
Lithium Sulfur Batteries, which react by connecting the anode composed of Lithium to the Sulfur / Cabon-based cathode during discharge, are Lithium batteries with the highest known energy density.
Since the depletion of sulfur caused by the dissolution of sulfur in the cathode in the electrolyte is the most fundamental problem, in this technology, there are successful studies on the development of polysulfide electrolytes that will minimize the loss of sulfur and the development of the carbon in the cathode as a nano wire. In addition, the charging and discharging characteristics are non-linear, requiring these batteries to be charged / discharged with microprocessor support.
The main problem of this type of battery was that the cycle life was very low compared to other Lithium battery types. However, in the studies carried out in 2013 and 2014, energy density and power density are compromised and 1500 cycle lives (400 mAh / gr - 0.5C charge / 1C discharge)
- High energy density (300-500 Wh / kg)
High charging efficiency (~ 99.7%)
Low cell voltage: 1.7-2.5V
- Average cycle life: 300 ... 800 cycles.

Basic chemical reaction
Discharge: S8 → Li2S8 → Li2S6 → Li2S4 → Li2S3
Charger: Li2S → Li2S2 → Li2S3 → Li2S4 → Li2S6 → Li2S8 → S8
Production is considered especially for military applications, portable devices and electric cars.
Lithium-Air Batteries ( Li-Air )
This battery type, which consists of Lithium and Lithium Oxide cathode / anode pair, does not contain electrolyte. Oxygen reduction at the anode with lithium oxidation at the cathode provides the necessary electron flow. Because Li-Air batteries use oxygen in the air, there is no need for "oxidizing material" and they are the most energy-dense Lithium battery types because less material is used. Discovered in the 1970s and considered for electric cars, Li-Air batteries could only make a leap forward with the development of metallurgical technology in the 2000s. The gravimetric energy density of Li-Air batteries is almost the same as that of Gasoline.
Studies are still ongoing on "Aqueous" types with aqueous solution between Li and LiO2 and "Solid State" types with Lithium permeable ceramic or polymer in between. Although commercial products with a sufficiently high power density and sufficient cycle life cannot be seen on the market, studies on Li-Air batteries have been increasingly continued in many battery research centers for the last 10 years.

Lithium-Ion Battery Technologies Comparison

Parametric Comparisons of Lithium Battery Chemistry:


Li4Ti5O12 (LTO)

LiNiMnCoO2 (NMC)

LiNiCoAl (NCA)

LiMn2O4 (LMO)

LiFePO4 (LFP)

LiCoO2 (LCO)
Source: batteryuniversity.com